Vertical Integration at Tesla
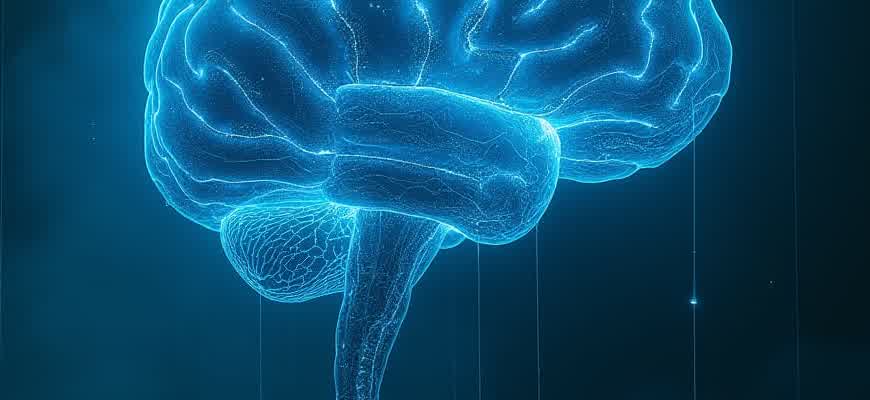
Tesla has become a prime example of how vertical integration can reshape the automotive industry. By controlling a significant portion of its production and supply chain, the company has minimized reliance on external suppliers, thus gaining greater control over costs, innovation, and quality. This strategy has allowed Tesla to rapidly scale its operations and adapt to market changes with greater agility.
Key Elements of Tesla's Vertical Integration:
- Battery production through Gigafactories
- In-house manufacturing of key components like electric motors
- Direct-to-consumer sales model
- Development of proprietary software and autonomous driving technologies
"Tesla’s approach to vertical integration is a key enabler of its technological and operational advantages, providing greater efficiency and the ability to innovate faster than traditional automakers."
This model contrasts sharply with the traditional automotive industry, where companies rely heavily on third-party suppliers for parts and assembly. Tesla's approach has allowed the company to create a seamless ecosystem that spans from design to final product delivery, minimizing external dependencies.
Aspect | Traditional Automakers | Tesla |
---|---|---|
Supply Chain Control | Outsourced parts and components | In-house production and ownership |
Innovation Speed | Slower, due to third-party dependencies | Faster, with full control over development |
Cost Efficiency | Higher due to middlemen | Lower, through economies of scale |
How Tesla Optimizes Its Supply Chain Through Vertical Integration
Tesla's strategy of vertical integration is a key factor in how the company manages its complex supply chain. By controlling a significant portion of the production process, from raw materials to finished products, Tesla reduces its dependence on third-party suppliers and gains greater control over costs, quality, and production timelines. This approach allows Tesla to ensure consistency in product design, improve production efficiency, and accelerate innovation.
Unlike many competitors, Tesla does not rely heavily on traditional supply chains. The company produces a substantial percentage of its components in-house, including batteries, electric drivetrains, and even software. Vertical integration offers Tesla the ability to respond quickly to market demands and technological shifts, positioning the company as a leader in the electric vehicle industry.
Key Aspects of Tesla's Vertical Integration
- Battery Manufacturing: Tesla operates Gigafactories that produce lithium-ion batteries for its vehicles, significantly reducing reliance on external suppliers.
- In-house Software Development: Tesla designs its own software, including the vehicle's operating system and autopilot capabilities, enabling deeper integration between hardware and software.
- Automotive Parts Production: Tesla manufactures many critical vehicle components, including electric motors and drivetrains, ensuring consistency and performance standards.
- Energy Products: Tesla also produces solar panels and energy storage products, creating a unified ecosystem of clean energy solutions.
Advantages of Tesla's Approach
"Vertical integration allows Tesla to maintain a competitive edge by offering products that are uniquely tailored to its specifications, making it less vulnerable to disruptions in the supply chain."
- Cost Control: By producing key components in-house, Tesla reduces costs associated with outsourcing and third-party suppliers.
- Supply Chain Resilience: Tesla mitigates risks from global supply chain disruptions, ensuring that key materials and components are readily available for production.
- Faster Innovation: Vertical integration allows for rapid iteration and improvements in product design, ensuring that Tesla remains at the forefront of automotive technology.
Table: Tesla’s Major Vertical Integration Areas
Area | In-house Production | Benefits |
---|---|---|
Battery Manufacturing | Gigafactories | Reduces costs, ensures supply stability, enables faster product development |
Software Development | Autopilot, vehicle OS | Deeper integration between hardware and software, continuous updates |
Vehicle Components | Electric motors, drivetrains | Improved performance, consistent quality |
Energy Products | Solar panels, storage | Creation of a unified ecosystem, energy independence |
Impact of In-House Battery Production on Tesla’s Cost Structure
Tesla’s strategy of producing its own batteries has significantly influenced the company’s cost structure, enhancing its profitability and operational control. By vertically integrating the battery production process, Tesla has reduced its dependency on external suppliers, creating more predictable costs and supply chain efficiencies. This shift has allowed the company to better control the pricing of one of the most critical components in electric vehicle (EV) production: the battery. Tesla’s approach to manufacturing batteries internally has helped lower the overall cost per unit, improving the margins on its EVs.
Internally manufacturing batteries has provided Tesla with multiple financial advantages. The reduction in external procurement costs is a key driver, but Tesla’s investment in research and development (R&D) has also enabled the company to innovate and produce more energy-dense, cost-efficient batteries. In the long term, this could enable further price reductions for consumers while maintaining profitability for Tesla.
Key Factors Affecting Tesla’s Cost Structure Through In-House Battery Production
- Material Cost Reduction: By controlling the supply chain and materials used for battery production, Tesla can optimize costs and minimize price fluctuations driven by third-party suppliers.
- Manufacturing Efficiency: With in-house production, Tesla has more control over the manufacturing process, leading to improved economies of scale and cost reductions as production volumes increase.
- Supply Chain Stability: Reducing reliance on third-party suppliers helps mitigate risks associated with supply chain disruptions, such as price hikes or delays, which would otherwise raise costs.
- R&D Investment: By investing in its own technology and developing proprietary battery systems, Tesla has been able to improve the energy density and performance of its batteries, which translates into a higher return on investment in the long run.
Impact on Tesla’s Profit Margins and Pricing Strategy
“By shifting battery production in-house, Tesla is positioning itself for long-term cost advantages, allowing for better margins and pricing flexibility in a competitive EV market.”
The shift to in-house battery production allows Tesla to pass on cost savings to customers, potentially lowering the base price of their vehicles. However, the strategic move also aligns with Tesla's overall goal of achieving sustainability and reducing carbon emissions. The company can achieve these goals without significantly impacting its profitability, as the cost reduction benefits are substantial over time.
Comparison of Cost Structures Before and After In-House Battery Production
Cost Factor | Before In-House Production | After In-House Production |
---|---|---|
Battery Procurement | Dependence on third-party suppliers | Self-manufactured batteries, reducing supplier markups |
Material Costs | Subject to market fluctuations | Better control over raw materials, lower costs |
Manufacturing Costs | Outsourced production | More efficient, streamlined in-house processes |
R&D Investment | Limited internal innovation | Higher focus on internal development and innovation |
Tesla’s Strategy for Software Development and Over-the-Air Updates
Tesla’s approach to software development is deeply integrated into its broader strategy of vertical integration. By developing its own software in-house, the company is able to have more control over product features, security, and updates. This autonomy allows Tesla to constantly refine and improve its vehicles' performance, even after the cars leave the factory. The ability to release new software features, fix bugs, and optimize performance remotely is one of Tesla's most significant competitive advantages.
At the core of this strategy lies Tesla’s use of over-the-air (OTA) updates. These updates allow the company to deliver new software features, system improvements, and even performance boosts without requiring customers to visit a service center. As a result, Tesla is able to maintain a consistent, high-quality user experience, while reducing costs related to physical service appointments. The ability to continuously upgrade vehicles with minimal disruption is a key differentiator in the electric vehicle market.
Key Elements of Tesla’s Software Development Approach
- Centralized Software Team: Tesla relies on an in-house team of software engineers to develop vehicle firmware and associated apps.
- End-to-End Control: Unlike traditional automakers that outsource software development, Tesla controls every aspect of the software stack, from low-level firmware to user interfaces.
- Rapid Iteration: Tesla’s agile development practices allow for fast-paced iteration and testing of new features.
Over-the-Air (OTA) Updates Process
Tesla's OTA updates follow a seamless, automated process that brings improvements directly to the car. Here's how it works:
- Vehicle Diagnostics: The car constantly collects data on its performance and sends it to Tesla's servers.
- Update Announcement: When new features or fixes are available, Tesla notifies users via the mobile app.
- Automatic Installation: Once an update is downloaded, the vehicle automatically installs it, typically during periods when the car is not in use.
- Post-Update Testing: After installation, the car runs a diagnostic to ensure the new software is functioning properly.
Benefits of OTA Updates
Tesla’s OTA updates allow them to push new features and improvements to vehicles remotely, ensuring a seamless and constantly evolving user experience without requiring customers to visit service centers.
Performance Enhancements Through OTA Updates
Feature | Impact |
---|---|
Acceleration Boost | Improved vehicle acceleration by up to 50%, delivered remotely. |
Autopilot Updates | Continuous improvements in self-driving capabilities via real-time updates. |
Battery Management | Optimized battery charging and longevity through software improvements. |
How Vertical Integration Enhances Tesla’s Quality Control
Tesla’s approach to vertical integration allows the company to maintain greater oversight over the entire production process. By controlling key stages of manufacturing–from battery production to vehicle assembly–Tesla reduces the risks associated with third-party suppliers and can immediately address issues as they arise. This self-sufficiency ensures more consistent product quality, higher levels of precision, and faster implementation of improvements.
The company’s in-house development and manufacturing capabilities also enable a seamless flow of information across different stages of production. This results in a more effective quality control system, where feedback from one department can quickly be implemented in another. Tesla’s integration helps it to swiftly identify defects and inefficiencies, often before they reach the consumer. As a result, they are able to enhance the durability, reliability, and overall performance of their vehicles.
Key Benefits of Vertical Integration on Quality Control
- Improved consistency: Direct control over the supply chain allows Tesla to standardize processes and minimize variability in product quality.
- Faster response times: Issues in production can be detected and resolved more quickly without waiting for external suppliers to intervene.
- Better resource allocation: Tesla can optimize its internal processes and adjust production priorities in real-time, maintaining high standards.
"By managing critical components and systems in-house, Tesla reduces its dependency on external suppliers, allowing for more rigorous quality checks and faster iteration of improvements."
Case Study: Tesla’s Battery Production
One of the most notable examples of vertical integration improving quality control is Tesla’s battery manufacturing process. Tesla produces its own battery cells at the Gigafactories, rather than relying on external suppliers. This enables the company to:
- Monitor the production environment: Ensuring that all materials used are up to their standards and preventing any defects from external sources.
- Enhance design flexibility: Quickly adapting battery designs to improve performance and safety based on internal feedback.
- Reduce failure rates: In-house production allows for rigorous testing before cells are incorporated into vehicles.
Comparison of Tesla's Integration vs. Traditional Automakers
Aspect | Tesla | Traditional Automakers |
---|---|---|
Control Over Supply Chain | High, with significant in-house production | Low, reliant on external suppliers |
Response to Quality Issues | Rapid identification and resolution | Slower, dependent on third-party involvement |
Quality Assurance | Extensive internal quality checks | Outsourced quality control procedures |
Leveraging Vertical Integration for Faster Product Development Cycles
Tesla’s strategy of vertical integration plays a critical role in accelerating the development of new products. By controlling the entire supply chain, from the design and manufacturing of vehicle components to the production of software and battery technology, Tesla is able to reduce the time required to bring innovations to market. This integrated approach not only shortens development timelines but also enhances the company’s ability to respond quickly to market needs and technological advancements.
One of the most notable outcomes of vertical integration at Tesla is its ability to iterate on product designs rapidly. With control over critical elements of the production process, Tesla can test and refine its vehicles, energy solutions, and software in-house without relying on third-party suppliers. This has allowed the company to reduce the typical development cycle that is common in the automotive industry, ensuring faster delivery of cutting-edge products.
Key Factors of Vertical Integration for Faster Development
- End-to-End Control: By overseeing the entire process from manufacturing to software integration, Tesla ensures that each component meets its standards without waiting for external suppliers.
- Rapid Prototyping: In-house manufacturing allows Tesla to quickly produce prototypes, which are essential for real-time testing and improvements.
- Data Utilization: Direct access to real-time data from its vehicles allows Tesla to immediately make software updates and enhance performance features.
- Supply Chain Optimization: Tesla’s ability to secure its own supply chains ensures that production timelines are not delayed by external vendors.
"Tesla’s ability to develop new products quickly is largely due to its strategic approach of controlling every stage of the product lifecycle. This control allows for continuous feedback and adjustments in real time, something traditional automakers struggle to replicate."
Comparison of Product Development Cycle: Tesla vs. Traditional Automakers
Factor | Tesla | Traditional Automakers |
---|---|---|
Design & Prototyping | In-house, rapid prototyping with immediate feedback | Outsourced, slower iteration processes |
Supply Chain | Direct control, reducing reliance on third-party suppliers | Dependent on external suppliers, risk of delays |
Software Updates | Frequent, over-the-air updates with real-time data | Limited, dependent on dealerships for updates |
Scaling Tesla’s Manufacturing: The Role of Gigafactories
Tesla's manufacturing expansion relies heavily on the strategic placement and development of its Gigafactories. These massive production facilities are designed to address both the growing demand for electric vehicles and energy products while achieving economies of scale. Each Gigafactory serves multiple purposes, from assembling vehicles to producing battery cells and other critical components. This integrated approach allows Tesla to reduce dependency on external suppliers and lower costs, all while controlling quality and innovation within its supply chain.
Through the Gigafactories, Tesla not only scales production but also achieves greater vertical integration. By producing key materials and components in-house, Tesla can drive down costs and gain a competitive advantage. The factories are a critical part of Tesla’s ability to ramp up production quickly, support the transition to sustainable energy, and maintain its leading position in the electric vehicle market.
Key Elements of Gigafactories’ Impact on Scaling Production
- Production Efficiency: Gigafactories are designed to streamline manufacturing processes, from battery production to vehicle assembly, ensuring a more efficient production cycle.
- Cost Reduction: By vertically integrating manufacturing, Tesla eliminates the need for middlemen and reduces production costs, allowing for more competitive pricing.
- Innovation and Flexibility: The scale of Gigafactories provides room for rapid innovation in vehicle design and manufacturing processes, allowing Tesla to stay ahead in technology.
Benefits of Vertical Integration through Gigafactories
"Tesla’s Gigafactories represent a significant step in reducing the costs of electric vehicles, pushing the boundaries of what’s possible in manufacturing efficiency, and accelerating the global transition to sustainable energy."
Vertical integration at Tesla ensures that a large portion of its production is controlled internally, allowing the company to make faster adjustments to market demands and technological developments. This internal control leads to shorter development cycles and faster innovation, reducing the time needed to bring new products to market.
The company’s Gigafactories not only meet the demand for electric vehicles but are essential in Tesla's strategy to manufacture energy storage products, solar panels, and other renewable technologies. This holistic approach to manufacturing creates a synergetic environment where all components work together seamlessly to support Tesla’s growth ambitions.
Gigafactories at a Glance
Gigafactory Location | Primary Function | Production Capacity |
---|---|---|
Shanghai, China | Vehicle manufacturing, battery production | 500,000 vehicles/year |
Berlin, Germany | Vehicle manufacturing, battery production | 500,000 vehicles/year |
Austin, Texas | Vehicle manufacturing, battery production | 500,000 vehicles/year |
Fremont, California | Vehicle manufacturing, battery production | 500,000 vehicles/year |
The Environmental Impact of Tesla’s Integrated Business Structure
Tesla's business model revolves around significant vertical integration, which offers numerous advantages in terms of sustainability. By controlling its production processes, Tesla reduces the environmental footprint of its operations and products. This strategy enables the company to optimize manufacturing techniques, materials sourcing, and product life cycles, ensuring that sustainability is embedded throughout the process.
The company's approach minimizes the need for third-party suppliers and transportation, cutting down on the carbon emissions associated with logistics. Furthermore, vertical integration allows Tesla to maintain strict quality control, reducing waste and ensuring the efficiency of energy consumption across its manufacturing and energy storage systems.
Reduction of Carbon Footprint Through Direct Control
- Optimized Manufacturing: By controlling production from the ground up, Tesla minimizes inefficiencies and reduces energy consumption during manufacturing.
- Lower Transportation Emissions: Vertical integration reduces reliance on external suppliers, decreasing the emissions from logistics and transportation.
- Efficient Resource Use: Tesla's direct control over resource procurement allows for better management of raw materials, reducing waste and promoting recycling.
Tesla’s strategy of producing batteries in-house not only reduces dependency on external suppliers but also ensures more sustainable and ethical sourcing of materials.
Environmental Benefits of Tesla's Energy Products
Tesla's energy products, such as solar panels and Powerwall, also benefit from vertical integration. This structure enables the company to incorporate renewable energy solutions into its production systems, enhancing the environmental value of its products. By manufacturing both electric vehicles and energy storage solutions, Tesla contributes to a cleaner, more sustainable energy ecosystem.
- Energy Independence: Tesla's solar products and energy storage systems work together to reduce reliance on fossil fuels and minimize energy waste.
- Recycling and Reuse: The company’s recycling programs for batteries and solar panels further reduce environmental impact, promoting a circular economy.
Vertical Integration Aspect | Environmental Impact |
---|---|
Battery Manufacturing | Lower emissions and more sustainable material sourcing |
Energy Production (Solar and Storage) | Reduction in fossil fuel dependency and waste reduction |